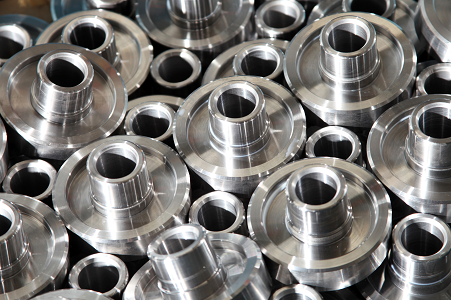
Cast Steel has become an increasingly important part of NovaCast’s business over recent years. The combination of excellent design, project management and quality assurance skills at our UK foundry with the low-cost, high-quality, high-capacity capabilities of our Far Eastern partners has allowed us to compete for and win many prestigious cast Steel projects.
Although we can cast a very wide variety of both Carbon and Stainless Steels, the bulk of our castings are in the most popular grades. For cast Carbon Steel, these include SA216 in both standard (WCB) and lower Carbon (WCC) grades and SA352 in its low temperature form (LCC). Stainless Steel castings have become a real specialist area for NovaCast and our most popular cast Stainless Steel grades are CF3 and CF8, including their Molybdenum containing variants (CF3M and CF8M). We also cast more exotic grades including 332C13 which is a Duplex Stainless Steel.
The wide range of Steel grades we cast gives a correspondingly wide range of properties to meet many specialist applications. These properties are often inter-related and selecting for one desirable property; ductility for example, will result in a reduction in other desirable attributes, such as hardness. We encourage our customers to engage with us at the earliest opportunity to allow us to advise on the optimum alloy selection to achieve the desired performance criteria.
The physical properties of cast steel will also change significantly depending on chemical composition and heat treatment used.
When selecting a Steel alloy for a cast component, the following must be considered:
- Hardness – how resistant to abrasion does it need to be? The Carbon content of the Steel determines the maximum hardness it is possible to achieve.
- Strength – how much force should the alloy be able withstand before deformation? Once again, Carbon is the most important element here. Greater hardness results in greater strength.
- Ductility – how much does the alloy need to deform under tensile stress before it fails? There is an inverse relationship between the amount of Carbon (and resulting hardness) and the ductility of the alloy.
- Toughness – how important is it that the alloy can withstand stress? Toughness can be adjusted with the addition of alloying metals and heat treatment. Increased ductility is usually associated with better toughness.
- Wear resistance – what rate of surface material loss is acceptable from surface-to-surface rubbing with other components? The addition of alloying elements, such as Molybdenum and Chromium, can increase the wear resistance of cast steels dramatically.
- Corrosion resistance – what working environment will the alloy be exposed to? Carbon Steels can be susceptible to corrosion but when alloyed with Chromium and Nickel, Stainless Steels are created which can be highly corrosion-resistant. Low alloy cast Steel’s corrosion resistance can, however, be improved by alloying with small amounts of copper.
- High-temperature properties – will the component be used at elevated temperatures? This can be significant as the mechanical properties of Steels are degraded as operating temperatures rise. This can lead to early failure due to oxidation, hydrogen damage, sulphite scaling, and carbide instability.
- Low-temperature properties – will the component be used at low temperature? This can be significant as the toughness of cast Steel is severely reduced at low temperatures. In special low-temperature Steels, this issue is addressed by adding alloying elements and through specialist heat treatments which improve a casting’s ability to withstand stresses and loads at lower than ambient temperatures.
- Machinability – is post-casting machining needed? Machinability is influenced by hardness, strength, thermal conductivity and thermal expansion. It is important, therefore, to take this requirement into account in addition to the other performance parameters.
- Weldability – will the component form part of an assembly where subsequent welding is required? If so, this should be considered as some Steel alloys are considerably more difficult to weld without defects than others. Weldability is primarily dependent on the steel casting’s chemical composition and heat treatment.
For help and advice or to discuss your requirements, call a member of NovaCast’s team on +44 (0) 1225 707466, send us a message here or email sales@novacast.co.uk.