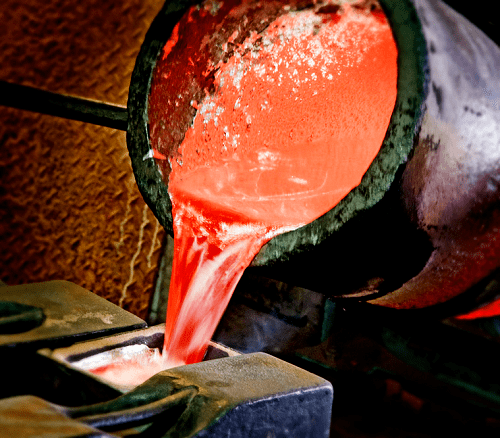
We often say that casting molten metal is like handling a living thing. Understanding how different alloys will react to different casting processes, component geometry, running systems, temperatures, etc. is part of the art of the foundry engineer. In recent years, the wealth of experience built up at the NovaCast Foundry has been enhanced by the addition of computer-based technologies, such as Casting Simulation and 3D Modelling software. Today, these technologies can shorten lead times from initial design submission to finished, cast component considerably but there is much that design engineers need to be aware of when considering the geometry of cast components.
Key amongst these considerations, is shrinkage. Shrinkage occurs at various stages of the casting process and must be carefully accounted for if component specifications are to be met and casting defects avoided.
In this article, we consider the various kinds of shrinkage and discuss how they influence the casting process.
Solidification Shrinkage
As molten metal cools, shrinkage occurs in three distinct stages:
- Liquid shrinkage is the contraction that occurs as the alloy cools but remains in its liquid state. This is not normally significant from a casting design perspective.
- Liquid-to-solid shrinkage (also known as solidification shrinkage) occurs as the alloy changes from a liquid to a solid. This is significant for the designer as it gives rise to the need to keep fluid metal channels open throughout the mould during cooling as contraction will draw more metal into the casting from the risers.
- Solid shrinkage is the continued shrinkage that occurs as the solid metal casting cools to ambient temperature in its solid state. This is also significant from the designer’s point of view. It is known as “Patternmaker’s Shrinkage” and must be compensated for within the tooling or mould design to ensure that the specified final overall dimensions are achieved.
Just as important from a casting geometry design perspective is the further classification of alloys by the type of solidification that occurs. There are three kinds as detailed below;
- Eutectic Solidification: These alloys remain in liquid form briefly in the mould but as soon as they start to cool solidification takes place rapidly throughout the casting. Internal shrinkage is minimal so risers are not so important as little additional alloy will be drawn into the mould. Examples or Eutectic alloys are Grey Iron, Aluminium 356, Silicon Bronze, Yellow Brass, Titanium and Zirconium.
- Directional Solidification: These alloys start to solidify quickly from the mould walls inwards. This makes them predictable and so good geometry design can take account of thermal gradient patterns to avoid closed pathways which could lead to internal shrinkage. Examples of Directional alloys are Carbon and Low Alloy Steel and Magnesium ZE43.
- Equiaxed Solidification: These alloys are somewhat unpredictable as they will start to solidify from the mould walls inwards but will also solidify in random internal islands which can block pathways. Fine, dispersed micro-porosity is typical of these alloys. Examples of Equiaxed alloys are Aluminium 356 and Aluminium Bronze.
Clearly, in order to take account of the magnitude and form that the shrinkage will take for a specific component geometry it is necessary to first select the alloy to be used for the casting.
Understanding the kinds of thermal patterns and solidification processes that will take place for each alloy is vital as it allows the designer to predict how solidification should occur. There are, however, additional complications even with the most predictable directional solidification. There will be differential cooling between cooler areas, where the mould surface area to metal volume is high, and other hotter areas, perhaps where metal volume is higher. Solidification will then travel inwards from the walls and from cooler to hotter areas. It is important, therefore, that the geometry allows for a clear liquid metal pathway to the hotter areas before solidification cuts them off from the riser. This is done through tapering and effective riser placement, without which, isolated internal shrinkage can occur giving rise to voids or pores.
Whichever type of solidification occurs, Solid Shrinkage will result in an overall and relatively predictable contraction to the final size at ambient temperature. This must be allowed for in the construction of the patterns, dies or coreboxes for mould making. It is important to note, however, that contraction may not be evenly distributed throughout the component as some areas may be stiffer than others. This can lead to the introduction of residual stresses and warping of the component unless the geometry design takes account of this risk.
Working closely with NovaCast’s Foundry Engineers or taking advantage of our in-house engineering design expertise can help to reduce lead times and cost, and ultimately improve the design of the cast component.
If you are investigating the best option for a cast or machined component and need to call on our experience and expertise we would be delighted to hear from you. Call a member of NovaCast’s team on +44 (0) 1225 707466, send us a message here or email sales@novacast.co.uk.