Metal Passivation – what it is and how it is used in metal casting
Passivation is a process used to protect metals against corrosion by creating a protective oxide layer on the surface of the metal. The objective is to shield reactive metals from damaging chemical reactions by creating an inert, or passive barrier between the metal and the surrounding environment. Passivation is used across a wide variety of applications and industries.
Before looking in more detail at passivation, it is worth briefly looking at corrosion; the reason we need to pacify metals in the first place.
What is corrosion?
Corrosion of metal occurs because of the interaction between active metal alloys and their environment. The interaction happens at a molecular level as the surface of the metal alloy reacts to become more chemically stable, resulting most commonly in the formation of oxides, hydroxides, and sulphides. The gradual decomposition of the metal alloy at its surface can be a purely chemical reaction, as in the rusting of iron on exposure to water and air, or it could be the result of electrochemical reactions. An example of this would be galvanic corrosion – when two dissimilar metals are together in a corrosive liquid – such as saltwater – and they create a charge which severely corrodes one of the two metals.
Not all metals are susceptible to corrosion to the same degree. The active potential of metals can be checked using the galvanic scale or anodic index, which grades metals based on their chemical instability and consequent reactivity. This shows that gold and silver are the least reactive with cast iron, mild steel, aluminium, and zinc sitting towards the more reactive end of the scale.
What is Passivation?
Passivation is the process of creating a thin passive layer over the entire surface of the metal object, making reactive metals less susceptible to environmental corrosion.
This passive layer could be applied as a micro coating, generated through a chemical reaction, or it could occur by spontaneous oxidation in the air. The passivation layer lowers the material’s chemical reactivity, enhancing its resistance to corrosion without altering the base metal.
It should be noted, however, that passivation does not improve the surface finish of metal parts. Passivation does not remove scale, or discoloration in the heat-affected zone for welded or brazed components.
What Materials can be Passivated?
Passivation is important in metal casting because it can be successfully applied to improve the performance of the most commonly cast alloys:
Stainless Steel
Stainless steels possess inherent corrosion resistance due to their chromium content which creates a protective passive chromium oxide layer when it is exposed to oxygen. Stainless steels are not entirely immune to rust formation, however, as various surface contaminants, such as free iron can break down the passive layer, as can heating during the welding process. Passivation using nitric or citric acid can effectively restore the passive layer.
Aluminium
Passivation of aluminium alloys is typically achieved through chromate conversion coating or anodizing, although plating, painting, and other barrier coatings are also used to create the inert layer. Chromate conversion can also be used to passivate tin, zinc, cadmium, copper, silver, and magnesium alloys.
Ferrous Alloys
Passivation can provide some protection to ferrous materials, such as steel, through the induction of oxidisation (rust) on the surface. The oxidisation is then transformed into metalophosphate using phosphoric acid and subsequent surface coatings can improve protection.
Titanium
When anodised, the passive layer of titanium oxide that quickly forms on exposure to air, can be thickened, which enhances protection. Passivation will remove the surface contaminants which are often left behind during manufacturing processes while enhancing the protective titanium oxide layer. As with other metals, thin-film interference produces a change in surface colour that will vary with the thickness of the passivation layer.
Nickel and Nickel Alloys
Inconel and Monel are nickel-based alloys known for their exceptional strength and corrosion resistance. Inconel contains a significant amount of chromium, so it naturally forms a strong chromium oxide layer to protect the material against corrosion. Monel has high levels of nickel and copper, giving it exceptionally high corrosion resistance, particularly against seawater.
During manufacturing process, however, surfaces may come into contact with iron particles and other contaminants, or welding, which interfere with the passive layer, making them less resistant to corrosion. Passivation is, therefore, recommended following manufacturing processes using these alloys.
When should passivation be used?
There are many situations that give rise to the need for passivation including:
After mechanical machining operations
This is of relevance to cast components that require surface finishing. Machining operations, such as cutting, grinding, linishing, fettling, and polishing, can damage or remove the passive layer on the metal component’s surface. Although the passive layer can self-restore, the changes in layer thickness may result in corrosion starting in the part. Passivation should always take place after mechanical finishing has been completed.
Immediately before stainless steel parts go into service
It is good practice for stainless steel parts to be passivated immediately prior to being put into operation to ensure that the passive layer is entirely intact and providing maximum protection.
After welding
By its nature, welding will frequently produce a heat-affected zone in surrounding metal. This heat-affected zone can damage the chromium oxide layer on stainless steels and add contaminants. The result is often seen around welded joints on stainless steel components where oxidisation is markedly worse than the rest of the component. Passivation can restore the passive layer and improve oxidation resistance.
Preventive maintenance
Passivation can also be done regularly as preventative maintenance to ensure that passive layers are restored as they can degrade over time through wear, contamination, abrasion, and weathering.
The Advantages and Disadvantages of Passivation
Passivation is a quick and cost-effective process that can increase the lifespan of cast and fabricated components. There are numerous potential advantages and disadvantages of passivation, including:
Advantages:
Corrosion prevention. The primary purpose of passivation is to create, enhance, or maintain a protective passive layer on a metal component’s surface which prevents or reduces corrosion. This helps improve and maintain the durability and longevity of metal components.
Wear resistance. The passive layer can make metal surfaces more resistant to wearing down from friction and abrasion. This can extend the service life of metal parts.
Reduced maintenance. Regular passivation reduces the need for system shutdowns and maintenance, resulting in lower costs and less system down-time.
Lower product contamination risks. The process eliminates chemically reactive iron and other contaminants.
No power source needed to maintain protection. As a spontaneous chemical reaction, passivation does not require an external power source to maintain the passive layer, making it simple and cost-effective.
Disadvantages:
Only works on some metals/alloys. Only metals that spontaneously form passive oxide films, like stainless steel, aluminium, and titanium, can be passivated. Other metals may require different anti-corrosion treatments.
Degraded through abrasion. The protection provided by the passive layer reduces as the layer is worn off through friction or abrasion over time. The only way to maintain protection would be to re-passivate the metal from time-to-time.
Affected by high acid and alkaline. Passivation will be less effective in highly acidic or alkaline environments as they can degrade the passive film.
Surface preparation is essential. Metals must be thoroughly cleaned and prepared before passivation to enable the formation of a consistent, protective, passive layer.
Does not completely eliminate corrosion. Passivation slows corrosion but does not completely eliminate it in most cases. Periodic reapplication is needed for continued protection.
Surface finishing still needed: Passivation does not smooth metal surfaces. Any surface finishing must be completed prior to passivation.
Environmental impact: There is a risk of environmental contamination if the chemicals used in passivation are not effectively managed. Greater use of citric acid (rather than nitric acid) in stainless steel passivation is reducing this risk.
Specialised equipment needed: Specialised equipment, which can be expensive, is required and chemicals used in the process can present safety hazards if not managed properly.
Summary
Passivation plays a significant role in the metal casting industry. It can be used to enhance the performance and lifespan of components cast in the most common ferrous and non-ferrous alloys. Although often naturally occurring, natural passivation can take a long time or it can develop unevenly, with variations in the grain of the metal or in the presence of surface deposits. Active passivation methods, as discussed here, speed up and standardise the process allowing passivation to be incorporated into production processes.
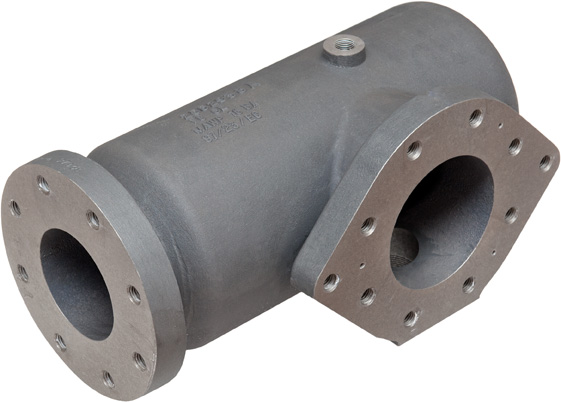