Shell Mould Casting
Shell mould casting is a metal casting process similar to sand casting, in that molten metal is poured into an expendable sand-based mould. However, in shell mould casting, the mould is a thin-walled shell created by applying a sand-resin mixture around a pattern. The pattern, a metal piece in the shape of the desired part, is reused to form multiple shell moulds. A reusable pattern allows for higher production rates, while the disposable moulds enable complex geometries to be cast.
Compared to sand casting, this process has better dimensional accuracy, a higher productivity rate, and lower labour requirements. It is often used for small to medium parts that require high precision.
Shell mould casting is used for both ferrous and non-ferrous metals. The most commonly used are cast iron, carbon steel, alloy steel, stainless steel, aluminium alloys, and copper alloys. Typical parts cast using this process are small-to-medium in size and require high accuracy, such as gear housings, cylinder heads, connecting rods, and lever arms.
Casting Design Considerations for Design Engineers
Some factors inherent in casting processes that can affect component design…
Why Use NovaCast Shell Mould Casting?
Shell mould casting delivers many benefits, including:
- It can be completely automated which lowers labour costs and facilitates mass production
- Good and consistent surface finishes result in lower machining costs compared to sand casting
- As no moisture is present in the shell, very few gases are produced and those that are escape through the thin shell walls easily as the sand is permeable
- The burning of the resin binder on the surface of the shell helps to make removal from the cast component easy
- The process allows complex shapes in a large range of sizes with good surface finish to be cast
- Little scrap is produced and what there is can be recycled. The sand-resin mix can be recycled by burning off the resin at high temperatures.
- Tooling costs are low and short lead times are possible
- A wide variety of metal alloys can be cast with this process
- Typical tolerances are just 0.005 mm/mm and the cast surface finish is 0.3–4.0 micrometers (50–150 μin) – this is better than with sand casting because a finer sand is used. The resin also assists in forming a very smooth surface.
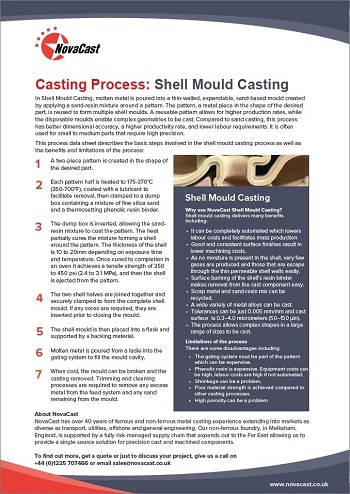
Shell Mould Casting Process
- A two-piece metal pattern is created in the shape of the desired part, typically from iron or steel. Other materials are sometimes used, such as aluminum for low volume production or graphite for casting reactive materials.
- Mould creation: Each pattern half is heated to 175-370 °C (350-700 °F) and coated with a lubricant to facilitate removal. The heated pattern is clamped to a dump box, which contains a mixture of fine silica sand and a thermosetting phenolic resin binder. The dump box is inverted, allowing this sand-resin mixture to coat the pattern. The heated pattern partially cures the mixture, which forms a shell around the pattern. Depending on the time and temperature of the pattern, the thickness of the shell is 10 to 20 mm. Each pattern half and surrounding shell is cured to completion in an oven giving it a tensile strength of 350 to 450 psi (2.4 to 3.1 MPa), and then the shell is ejected from the pattern.
- Mould assembly: The two shell halves are joined together and securely clamped to form the complete shell mould. If any cores are required, they are inserted prior to closing the mould.
- The shell mould is then placed into a flask and supported by a backing material.
- Pouring: The mould is securely clamped together while molten metal is poured from a ladle into the gating system to fill the mould cavity.
- Cooling: After the mould has been filled, the molten metal is allowed to cool and solidify into the shape of the final casting.
- Casting removal: After the molten metal has cooled, the mould can be broken and the casting removed. Trimming and cleaning processes are required to remove any excess metal from the feed system and any sand remaining from the mould.
Shell mould casting is a metal casting process similar to sand casting, in that molten metal is poured into an expendable sand-based mould. However, in shell mould casting, the mould is a thin-walled shell created by applying a sand-resin mixture around a pattern. The pattern, a metal piece in the shape of the desired part, is reused to form multiple shell moulds. A reusable pattern allows for higher production rates, while the disposable moulds enable complex geometries to be cast.
Compared to sand casting, this process has better dimensional accuracy, a higher productivity rate, and lower labour requirements. It is often used for small to medium parts that require high precision.
Shell mould casting is used for both ferrous and non-ferrous metals. The most commonly used are cast iron, carbon steel, alloy steel, stainless steel, aluminium alloys, and copper alloys. Typical parts cast using this process are small-to-medium in size and require high accuracy, such as gear housings, cylinder heads, connecting rods, and lever arms.
Limitations of the process
There are some disadvantages to the shell mould casting process including:
- The gating system must be part of the pattern because the entire mould is formed from the pattern, which can be expensive.
- The phenolic resin is expensive, although not much is required because only a shell is being formed.
- Equipment costs can be high
- Poor material strength is achieved compared to other casting processes
- Shrinkage can be a problem
- High porosity can be a problem.
- Secondary machining often required even though the surface finish is better than can be achieved with sand casting.
- Labour costs can be high if the process isn’t automated.
To discuss your requirements, call a member of NovaCast’s team on +44 (0) 1225 707466, send us a message here or email sales@novacast.co.uk.
Casting process comparison: Sand Casting vs Shell Mould Casting
This article compares Sand Casting and Shell Mould Casting, which uses phenolic resin to create a sand shell mould.
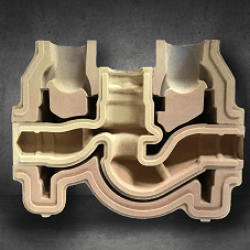
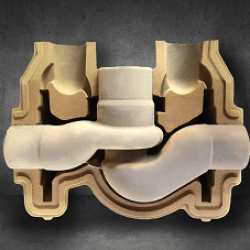
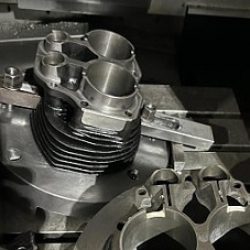
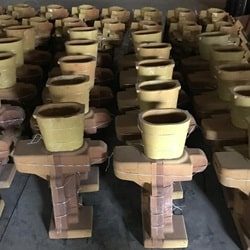