Aluminium is one of the most important raw materials used in metal casting due, in part, to its combination of versatility, relatively low weight, and high strength. It is used in castings across a wide range of industries from aerospace to automotive and electronics to renewable energy. At NovaCast aluminium is one of the primary alloys used across our range of casting processes.
One of the most common elements on earth
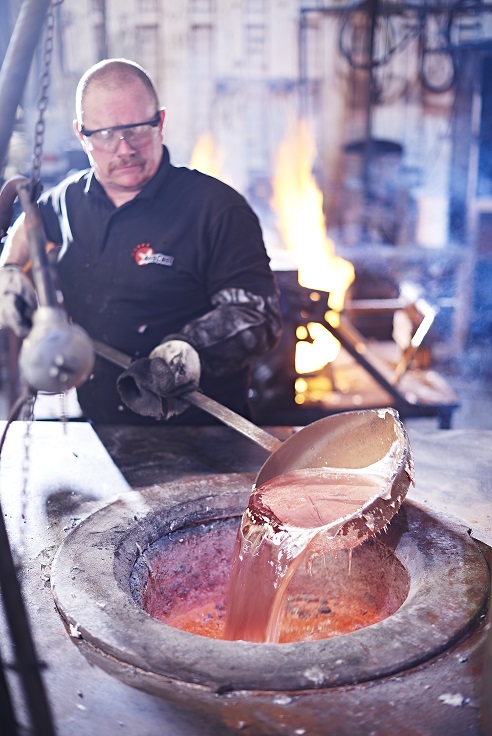
Aluminium is derived primarily from Bauxite ore and is the most abundant metal in the world, making up approximately 8% of the earth’s crust. It is, in fact, the third most common element after oxygen and silicon. Extraction of aluminium from Bauxite involves a chemical process that produces alumina (aluminium oxide), which then undergoes a smelting process to produce pure aluminium.
The whole extraction and smelting process is very resource-intensive with large amounts of electricity and water needed. Once produced, however, aluminium is extremely recyclable without any detriment to its mechanical properties, and the increasing use of renewably produced electricity is starting to reduce the environmental impact of aluminium production. At NovaCast, we ensure that there is very little waste in our production processes with excess material being routinely recycled.
The perfect casting alloy?
The ubiquity of aluminium within manufacturing processes is due to its unique properties. Pure aluminium is very light at just one third of the weight of steel or copper, it is also the second most malleable and the sixth most ductile metal. Pure aluminium at 90MPa is not particularly strong but what it lacks in strength it more than makes up for in its ability to alloy with most other metals to modify its mechanical properties.
Tensile strength can be increased considerably (to over 700MPa) to match that of some steels by adding alloying elements such as copper, silicon, manganese, magnesium, tin, and zinc. These alloys deliver excellent strength to weight ratios. And, unlike steel, the tensile strength of aluminium alloys actually increases at lower temperature whereas steel can become more brittle when exposed to low temperatures for long periods. At the same time, certain aluminium alloys can also withstand the highest operating temperatures. The alloying capabilities of aluminium are key here as such a wide range of performance criteria can be met by selecting the appropriate chemical composition. When combined with its inherent light weight, these alloys are perfect for applications such as aerospace, automotive, medical devices, and many more.
Another property that adds to the usability of aluminium is its corrosion resistance resulting from interaction with air at the surface, which forms a protective layer of aluminium oxide. This can be further enhanced by surface finishes, such as anodising, chromate conversion coatings, thermal spraying, chemical deposition, etc. Although aluminium also has excellent resistance to most acids it can be less resistant to alkalis, but surface treatments can be applied to enhance performance in this respect.
To further broaden its appeal and usability, aluminium also has excellent thermal and electrical conductivity, exceptional reflective properties, is non-toxic and odourless. It also provides excellent shielding against Radio Frequency Interference (RFI) and EMI (Electromagnetic Interference). And its high malleability and ductility mean that it can be pressed incredibly thin and easily formed into any shape.
Post-casting treatments
Specific properties can be further enhanced by post-processing treatments that can modify the performance characteristics. Hardening can be achieved through quenching and natural or artificial age hardening. Annealing can be used to improve pliability and make alloys less brittle, and solution heat treatment can also be used to make aluminium more pliable. Potential cracking issues can be mitigated by stress-relieving techniques such as heating at low temperatures then slow cooling.
A pleasure to work with?
These properties don’t just enhance useability in terms of applications, aluminium alloys have many benefits to the foundry as well. The thermal properties of these alloys ensure that heat dissipates quickly, which speeds up the production process. The relatively low melting temperature of aluminium alloys extends the range of casting processes that can be used to include permanent mould processes, such as die casting. Aluminium alloys are used by NovaCast across all of its casting processes, including sand casting, gravity die casting, high and low pressure die casting, investment casting, shell mould casting, and lost foam casting, which demonstrates the versatility of these alloys from a casting perspective. The high malleability properties allow foundries to produce complex aluminium castings at near net shape with excellent surface finishes.
So, what’s not to like about aluminium for metal casting?
On the face of it, aluminium would appear to be the answer to any question relating to the choice of casting material. There are, however, also some areas where aluminium is a less favourable choice and areas where it presents significant challenges.
High on the list of drawbacks is cost. Although aluminium is relatively cheap in its pure form, many of the advantages detailed above are delivered through the alloying process. Achieving the desired performance by alloying can often result in expensive aluminium variants that can often be more costly than other options, such as carbon steel. There is, however, a trade-off here. In automotive manufacturing, for example, the higher costs are offset by reduced weight and recyclability, which helps operating efficiency and meets sustainability targets.
Aluminium also presents some production challenges. Shrinkage during cooling can be significant and this can result in cracks, breakages, and internal casting defects. Liquid aluminium also holds large quantities of gas, which can form internal bubbles and areas of weakness during the cooling process. These defects can compromise strength and reliability if they are not properly managed by the foundry and identified during post-casting testing.
Sustainability matters
While accepting that we operate in an industry that can have a major detrimental environmental impact, at NovaCast, we are committed to making our business, and those in our supply chain, as sustainable as we can. The high percentage of castings we produce using aluminium alloys helps in that objective.
Aluminium is one of the most sustainable casting materials. It is 100% recyclable with no loss of its inherent properties during that process. According to the UK Aluminium Federation, “The recycling of good quality aluminium scrap into new ingot takes place with an energy saving of 95% of the energy required to produce the same weight of aluminium through the primary smelter route”. In the UK, it is estimated that 75% of all the aluminium previously sold to consumers through transport, packaging, engineering, building, etc. is being recycled and used in new castings by foundries like NovaCast.
Always happy to help…
At NovaCast, we can produce castings across a wide range of casting processes using an equally wide range of alloys, both ferrous and non-ferrous. Ultimately, the choice of alloy will be dictated by engineering design, performance, and commercial considerations and we are always happy to provide guidance and advice to achieve project objectives.
If you are investigating the best option for a cast or machined component and need to call on our experience and expertise we would be delighted to hear from you. Call a member of NovaCast’s team on +44 (0) 1225 707466, send us a message here or email sales@novacast.co.uk.