Testing Options
Dimensional Accuracy
NovaCast has invested heavily over recent years in exceptionally accurate Mitutoyo and Faro Coordinate Measuring Machines (CMM) installed within a heat-controlled inspection facility in Melksham, Wiltshire. The combination of equipment available allows optimum flexibility whether measuring the most complex components to the tightest tolerances or simple components that need to be measured quickly. All castings are soaked for at least 24 hours prior to measuring.
The latest addition to our inspection facility is an 8 ft (2.4M), 6 Axis Faro Prime measuring arm, which is their most accurate contact measurement system, allowing the import of data and 3D files. This includes alignment, calibration, inspection, reverse-engineering and ‘as-built’ documentation with an accuracy of 16 microns. This is ideal for completing surface measurements and dimensional calculations to the highest degree of accuracy.
Mechanical Properties Testing
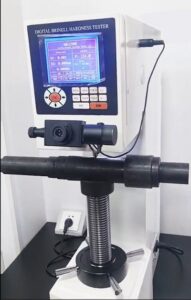
- Used to check that alloys and castings are within specification:
Hardness Testing: A non-destructive test giving a numerical value, which can be used to assess the machinability and wear resistance of an alloy. - Tensile and Impact Testing: Conducted on test specimens, these tests commonly measure ultimate tensile strength, yield strength, elongation and reduction of area data. Other tests can determine the ductility and strength of a sample by measuring the amount of energy absorbed during fracture.
- Service Load Tests: Conducted on the entire casting, these tests measure deflection when a load is applied. Hydraulic pressure tests can be carried out to destruction or a pre-determined proof load and spin tests can be used for rotating components.
Chemical Testing
These tests will determine whether the chemical composition of an alloy, which can have a large impact on the properties of the casting, are within specification. A specially cast sample is analysed using spectrographic atomic absorption or x-ray fluorescence.
Casting Integrity: Non-Destructive Testing (NDT)
The integrity or soundness of a casting can obviously have a dramatic impact on the performance of a cast component but very often defects can be hidden within the structure of the casting. Various Non-destructive tests can be specified by customers and undertaken by NovaCast to prove the integrity of castings prior to delivery:
- Visual Inspection: a variety of imperfections in a casting, such as sand holes, surface shrinkage, blowholes, etc. can be picked up by careful visual inspection so this is the starting point.
- Dye Penetration and Fluorescent Powder Testing: Used for both ferrous and non-ferrous metals, these tests can reveal tiny surface cracks, pores and other surface imperfections but cannot reveal internal defects.
- Magnetic Particle Inspection: Used to reveal small cracks at or near the surface of ferrous alloys by creating a strong magnetic field around the casting. Small metal particles are used to detect distortions in the magnetic field as defects and voids react differently to surrounding metal.
- Ultrasonic Testing: High frequency acoustic energy is transmitted into the casting and measurements of deflected energy can reveal the location and size of internal defects. This method can also be used to measure wall thickness and nodule count in ductile iron.
- Radiographic Inspection: Radiation from an x-ray tube is used to reveal internal defects as they absorb less radiation. The areas where less radiation has been absorbed are revealed on radiographic film.
- Eddy Current Inspection: Used to detect minor cracks and defects near the surface and discontinuities in the casting caused by material changes. This is a fairly expensive process and is limited to electrically conductive metals.
Pressure Testing: Where part of the specification is for a pressure-tight casting; air, water or inert gas are used to test the casting for leaks under pressure.
To discuss your requirements, call a member of NovaCast’s team on +44 (0) 1225 707466, send us a message here or email sales@novacast.co.uk.